- Chemical Spraying: The chrome like layer is applied by using two chemicals which react when atomising, creating silver nitrate (chrome effect) This step requires precision and often specialized equipment to ensure uniformity.
- Rinsing: After applying the chrome effect layer, the surface is rinsed to remove any unreacted chemicals.
The surface needs to be cleaned thoroughly to remove dust, oils, and any other contaminants that could interfere with adhesion. For smooth surfaces, light sanding is required. The prepared surface is sprayed with primer that will amplify the chrome effect finish that follows.
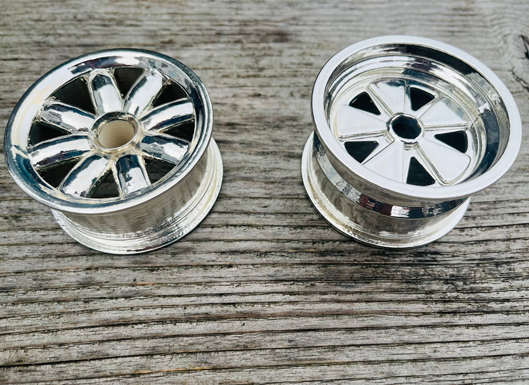
Spray coating Process:
Protective topcoat:
- Topcoat Application: A final protective topcoat is applied over the chrome effect finish to protect it from corrosion, scratches, and oxidation. This also gives the finish a deeper shine.
- The coated surface is then cured in our top of the range oven to ensure the topcoat hardens and bonds properly.
Key benefits of chrome spraying
- Environmentally friendly: Uses fewer hazardous chemicals compared to traditional chrome plating.
- Versatility: Works on non-metal surfaces and complex shapes that would be difficult to plate traditionally.
- Cost-effective: Generally, less costly and labour intensive than electroplating.
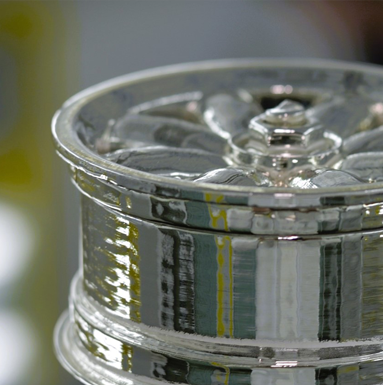
FAQs
Cleaning removes dust, oils, and contaminants that could interfere with the adhesion of the chrome effect.
get in touchColour tints are applied during the initial chroming process, enabling the creation of unique shades and effects.
get in touchChrome restoration is the process of repairing and refinishing chrome components to restore their original shine and brilliance. The process starts with an assessment of the chrome parts, followed by cleaning, repairing damage, and re-plating to ensure a flawless, mirror-like finish.
get in touchChrome restoration repairs dull or damaged parts, enhances durability, and restores the timeless elegance of your vehicle.
get in touchIt is created using two chemicals that react when atomised, forming silver nitrate, which gives the chrome effect.
get in touchThe topcoat protects the finish from corrosion, scratches, and oxidation, while enhancing its shine. The coated surface is cured in a high-performance oven to ensure the topcoat hardens and bonds effectively.
get in touchChrome Spraying Videos
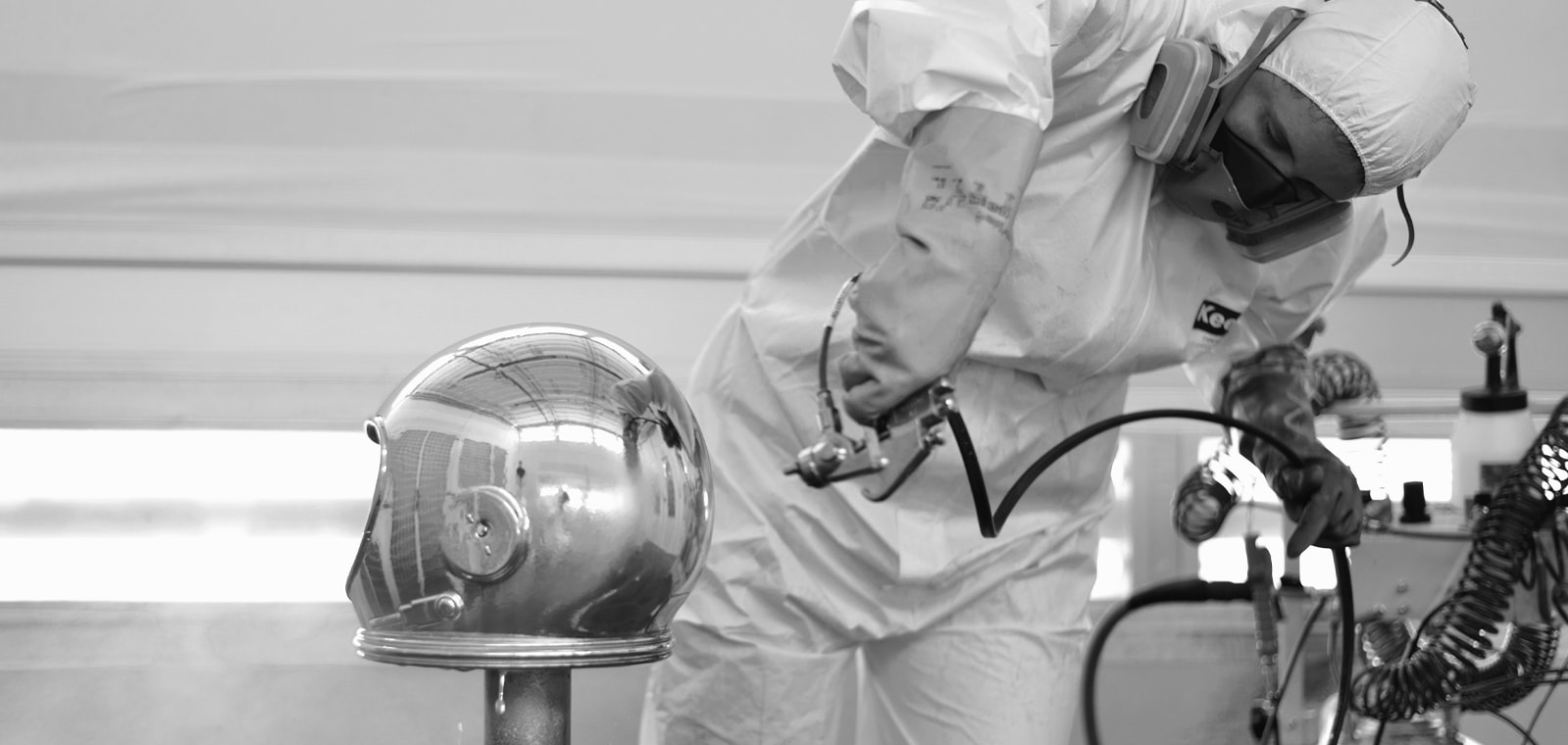
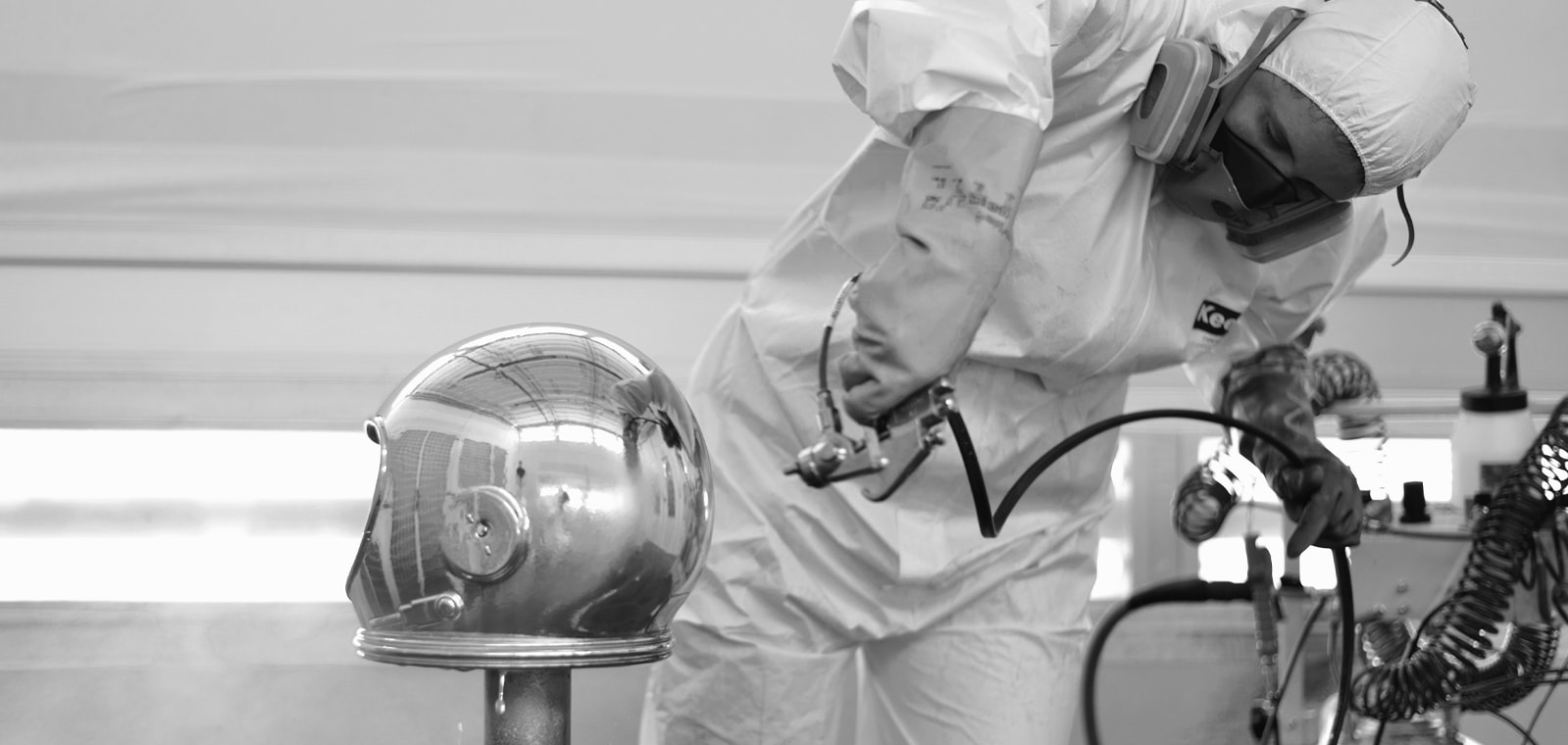